گاز محافظ یک جزء حیاتی در فرآیندهای جوشکاری است که به عنوان یک مانع محافظ برای جلوگیری از آلودگی جوی حوضچه جوش عمل میکند. گاز محافظ نقشی حیاتی در تضمین یکپارچگی و کیفیت جوش دارد و با ایجاد جوی پایدار در اطراف قوس جوشکاری، از ایجاد عیوبی مانند تخلخل، ترک خوردگی و اکسیداسیون بیش از حد جلوگیری میکند. به صورت کلی گاز محافظ منجر به ایجاد جوشهایی قوی و باکیفیت بالا میشود. اگر جوشکار هستید، یا میخواهید جوشکار شوید، باید با این گازها و نحوه کاربرد آنها در جوشکاری آشنا شوید، چرا که در هر فعالیت شغلی جوشکاری و در هر پروژه استفاده می شوند. در این مقاله همراه ابزار جوش و برش وینر باشید تا به بررسی کامل گاز محافظ بپردازیم.
تعریف گاز محافظ
در طی فرآیند جوشکاری، حوضچه جوش متشکل از فلز پایه و فیلر ذوب شده, ایجاد میشود. گاز محافظ از حوضچه جوش در برابر آلایندههای جوی مانند نیتروژن و هیدروژن محافظت میکند. جوش ایجاد شده بدون گاز محافظ، ضعیف بوده و پس از انجماد تخلخل دارد. گاز محافظ مانند یک پتو بر روی حوضچه جوش مذاب عمل کرده و آلایندههای جوی را خارج میکند. گازهای محافظ خنثی یا نیمه خنثی هستند و در فرآیند جوشکاری میگ و TIG مورد استفاده قرار میگیرند. در سایر فرآیندهای جوشکاری قوس الکتریکی از روشهای جایگزین برای محافظت جوش در برابر جو استفاده میشود – به عنوان مثال، در جوشکاری توپودری، الکترود حاوی شار بوده و به عنوان گاز نیمه بی اثر مورد استفاده قرار میگیرد.
تاریخچه پیدایش گاز محافظ
در طول دهه 1920 تحقیقات قابل توجهی در مورد محافظت از قوس و ناحیه جوش توسط گاز محافظ انجام شد. جو اکسیژن و نیتروژن در تماس با فلز مذاب جوش، باعث ایجاد جوشهایی شکننده و متخلخل میشد. محققان جوشهای ایجاد شده با گاز محافظ را آزمایش کردند. برای این کار نخستین بار الکساندر و لانگمویر در محفظههایی با استفاده از هیدروژن به عنوان جو جوشکاری کار کردند. آنها از دو الکترود استفاده کردند که با الکترودهای کربن شروع میشد اما بعداً به الکترودهای تنگستن تغییر یافت. هیدروژن در قوس به هیدروژن اتمی تبدیل شد. سپس از قوس خارج شده و شعله شدیداً داغ هیدروژن اتمی را تشکیل داد، در نهایت به شکل مولکولی تبدیل گردید و گرمای زیادی آزاد شد. این قوس دوباره نیمی از گرمای شعله اکسی استیلن را تولید کرد. در نهایت به فرآیند جوشکاری هیدروژن اتمی تبدیل شد.
جالب است بدانید که این فرآیند هیچگاه رایج نشد، اما به کمک این روش، کم کم گاز محافظ به شکل امروزی اختراع شد. با شروع جنگ جهانی دوم، این گازها از یک روش محلی به یک استاندارد تجاری تغییر پیدا کرد.
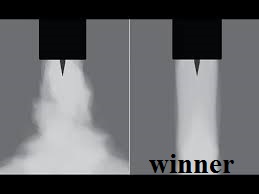
چرا استفاده از گازهای محافظ برای جوش اهمیت دارند؟
محافظ عمدتاً برای محافظت از فلز مذاب از آلودگی و اکسیداسیون ناشی از گازهای مضر در جو استفاده می شود. گازهایی که موجب آلودگی جوش می شوند عبارتند از :
- اکسیژن
- دی اکسید کربن
- نیتروژن
- بخار آب
آنها همچنین قسمت های مهمی از فرآیند جوشکاری را تحت تأثیر قرار می دهند ، این قسمت ها عبارتند از :
- ویژگی های انتقال فلز و قوس الکتریکی
- عرض منطقه همجوشی
- سرعت جوش
- نفوذ جوش
- الگوهای شکل سطح
خواص گازهای محافظ جوشکاری مختلف مورد استفاده در آموزش جوشکاری در پروژه های جوشکاری در دنیای واقعی کاربرد دارد و انتخاب گاز اشتباه می تواند منجر به نقص جوش، تخلخل و ناپیوستگی شود.
سایر دلایل اهمیت گاز محافظ در جوشکاری:
- جلوگیری از اکسیداسیون: گاز محافظ با ایجاد یک محیط بیاثر یا کماثر، از اکسید شدن فلز مذاب و ایجاد اکسیدهای مضر جلوگیری میکند. این اکسیدها میتوانند باعث کاهش استحکام جوش و افزایش تخلخل شوند.
- کاهش تخلخل: با جلوگیری از ورود گازهای اتمسفری به حوضچه مذاب، گاز محافظ از ایجاد حبابهای گاز در جوش و در نتیجه تخلخل جلوگیری میکند.
- بهبود خواص مکانیکی جوش: با حذف آلودگیها و ایجاد یک جوش تمیز و یکنواخت، گاز محافظ باعث بهبود خواص مکانیکی جوش مانند استحکام کششی، خستگی و چقرمگی میشود.
- کنترل شکل جوش: گاز محافظ با کنترل جریان فلز مذاب و ایجاد یک قوس پایدار، به شکلدهی بهتر جوش کمک میکند.
- افزایش سرعت جوشکاری: برخی از گازهای محافظ میتوانند سرعت جوشکاری را افزایش دهند و باعث کاهش هزینههای تولید شوند.
انواع گاز محافظ در جوشکاری
گازهای محافظ به صورت کلی به دو دسته بی اثر و نیمه بی اثر تقسیم میشوند. تنها گازهای نجیب هلیوم و آرگون مقرون به استفاده هستند و در جوشکاری مورد استفاده قرار میگیرند. این گازهای بی اثر در جوشکاری قوس الکتریکی استفاده میشوند. گازهای محافظ نیمه اثر یا نیمه خنثی یا فعال شامل دی اکسید کربن و اکسیژن هستند. بیشتر این گازها در مقادیر زیاد به جوش آسیب میزنند، اما زمانیکه به صورت کنترل شده مورد استفاده قرار گیرند، موجب ایجاد جوشهای تمیز و بدون عیب و نقص خواهند شد.
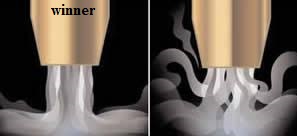
گاز محافظ بی اثر در جوشکاری
گاز محافظ بی اثر یا خنثی، به عنوان گازهای نجیب نیز شناخته میشوند. گازهای بی اثر، بی رنگ و بی بو هستند و واکنش های غیر شیمیایی دارند. با توجه به گران بودن گازهای نجیب، فقط گاز هلیم و آرگون مقرون بصرفه بوده و در فرآیندهای جوشکاری مورد استفاده قرار میگیرند.
گاز آرگون
آرگون 1 درصد هوا را تشکیل می دهد و محصول جانبی فرآیندهای تولید اکسیژن است. این گاز برای محافظت از جوش در حالت مسطح و در سطوح عمیق مناسب است. گاز آرگون یکی از پرکاربردترین گازهای محافظ در جوشکاری است. این گاز برای جلوگیری از اکسیداسیون فلزات و ایجاد محیط بیهوا در حین جوشکاری استفاده میشود. آرگون خالص اغلب با آلومینیوم و فلزات غیر آهنی استفاده میشود. این گاز برای محافظت از جوش های صاف و جوش در شیارهای عمیق خوب است.
گاز محافظ آرگون برای کاربردهای جریان متناوب (AC) و برای قوسهای طولانی تر در ولتاژهای پایین تر مناسب است. افزودن هلیوم خواص انتقال حرارت آرگون را بهبود میبخشد. آرگون مخلوط با دی اکسید کربن یا اکسیژن می تواند به تثبیت قوس ایجاد شده کمک کند.
گاز هلیوم
هلیوم، مانند آرگون خالص، به طور کلی با فلزات غیر آهنی، اما همچنین با فولادهای ضد زنگ استفاده میشود. از آنجایی که هلیوم یک پروفیل نفوذ گسترده و عمیق ایجاد میکند، به خوبی با مواد ضخیم کار میکند و معمولاً در نسبت های بین 25 تا 75 درصد هلیوم به 75 تا 25 درصد آرگون استفاده میشود.به صورت کلی گاز محافظ هلیوم نسبت به آرگون گرانتر است و به سرعت جریان بالاتری نسبت نیاز دارد. در فولادهای ضدزنگ، هلیوم معمولاً در فرمول سه مخلوط آرگون و CO2 استفاده میشود.
هلیوم برای کاربردهای جوشکاری مکانیزه مؤثر است اما برای جوشکاری دستی خیلی قابل استفاده نیست. از آنجا که هلیوم خالص یک قوس نامنظم ایجاد میکند، میتواند هنگام کار با فولاد باعث پاشیدگی جوش شود. با این وجود هلیوم خالص برای منیزیم، مس و آلومینیوم ایده آل است. هنگام مخلوط کردن با آرگون، هلیوم میتواند برای تمیز کردن کاتد استفاده شود.
گاز نیمه بی اثر در جوشکاری
گازهای دارای واکنش پذیری کم به عنوان نیمه بی اثر یا گاز محافظ نیمه خنثی شناخته میشوند. گازهای نیمه بی اثر که در فرآیند جوشکاری استفاده میشوند، عبارتاند از:
- هیدروژن
- اکسیژن
- دی اکسید کربن
- نیتروژن
از گاز محافظ نیمه اثر میتوان بصورت خالص یا به عنوان مخلوط استفاده کرد. هنگامی که مقادیر مناسبی از آنها در کار جوشکاری اعمال شود ، گازهای نیمه بی اثر میتوانند کیفیت جوش را بهبود بخشند.
گاز هیدروژن
گاز محافظ هیدروژن به یک گاز بسیار سبک و آسان برای جلوگیری از اکسیداسیون فلزات شناخته شده است. با این حال استفاده از گاز هیدروژن نیاز به دقت و دقت دارد، زیرا هیدروژن یک گاز قابل اشتعال است و در صورت عدم استفاده ممکن است خطراتی ایجاد شود؛ به همین دلیل گاز محافظ هیدروژن اغلب در ترکیب با سایر گازها استفاده میشود. با افزودن آرگون به گاز محافظ هیدروژن میتوان نفوذ را عمیق تر و سرعت جوش را افزایش داد. در درجه هایی از فولاد ضد زنگ که به اکسیژن حساس هستند، میتواند از این گاز استفاده کرد. به صورت کلی گاز محافظ هیدروژن سیالیت فلز را بهبود می بخشد، تمیزی سطح را افزایش میدهد و میتواند با نیکل و برخی فولادهای ضد زنگ استفاده شود.
هیدروژن گاز محافظ کاملی نیست، اگر به طور نادرست مورد استفاده قرار گیرد، میتواند باعث ایجاد تخلخل جوش شود. این پدیده توسط گازهایی که بیش از حد به دام افتاده اند ایجاد و منجر به ایجاد حفره های گرد میشود. از عوارض دیگر استفاده نادرست از گاز محافظ هیدروژن این است که ترک خوردگی جوش در فولادهای کربنی و آلیاژ کم بوجود میآید.
گاز نیتروژن
این گاز نیمه بی اثر بیشتر جو ما را تشکیل میدهد. مانند سایر گازهای نیمه خنثی، نیتروژن زمانی که با گازهای دیگر ترکیب شود بهترین استفاده را دارد. نیتروژن پایداری قوس و نفوذ جوش را افزایش میدهد. مخلوط های گازی حاوی نیتروژن میتوانند خواص مکانیکی را افزایش و از ایجاد تخلخل و ترک جلوگیری کنند. نیتروژن همچنین باعث افزایش نفوذ جوش و افزایش پایداری قوس میشود. گاز محافظ نیتروژن برای برخی از فولادهای ضد زنگ استفاده میشود، اما باعث ایجاد تخلخل در فولادهای کربنی میشود. ممکن است از نیتروژن خالص، هیدروژن-نیتروژن یا آرگون-دی اکسید کربن-نیتروژن استفاده شود. هنگام استفاده از آلیاژ حاوی نیتروژن، مخلوط گاز نیتروژن خواص مکانیکی را افزایش می دهد و از هدر رفتن نیتروژن از فلز جلوگیری میکند.
گاز اکسیژن
به صورت کلی هیچگاه از گاز محافظ اکسیژن به تنهایی استفاده نمیشود. زیرا باعث اکسیدن شدن فلزات شده و موجب ایجاد جرقه و آتش سوزی خواهد شد. به همینن دلیل از گاز اکسیژن به عنوان افزودنی به سایر گازها استفاده میشود. افزودن دو تا پنج درصد گاز محافظ اکسیژن به آرگون باعث افزایش پایداری قوس، کاهش کشش سطحی و افزایش خیس شدن فلز جامد میشود. به دلیل خواص اکسیداتیو نمی توان از آن برای جوشکاری آلومینیوم، منیزیم یا مس استفاده کرد. اکسیداسیون الکترود منجر به رسوب متخلخل (بدون اکسیدزدای کافی) می شود. به صورت کلی باید مقدار گاز محافظ اکسیژن کاملاً تعیین شده و کم باشد زیرا بیش از حد ممکن است باعث شکننده شدن جوش میشود.
مشابه هیدروژن، اکسیژن معمولاً با گازهای دیگر برای محافظت از جوش استفاده میشود. به عنوان مثال ، اکسیژن معمولاً در طول جوشکاری با آرگون برای بهره بردن از مزایای زیر استفاده می شود :
- تثبیت قوس
- به حداقل رساندن پاشش جوش
- بهبود انتقال فلز
گاز دی اکسید کربن
گاز محافظ دیاکسید کربن نیز یک گاز معمولی در جوشکاری است که به عنوان یک جایگزین ارزانتر برای آرگون استفاده میشود. این گاز برای جوشکاری فلزاتی مانند فولاد مناسب است.به خصوص در جوشکاری گاز بی اثر فلزی میگ (MIG) بسیار مفید است زیرا باعث افزایش سرعت جوش، نفوذ و خواص مکانیکی می شود. گاز محافظ Co2 انتقال حرارت خوبی دارد و جوش بسیار عمیقی ایجاد میکند، اما قوس تا حدودی ناپایدار است و از طرفی دیگر موجب افزایش پاشش نیز میشود. ترکیب آرگون-دی اکسید کربن رایج است زیرا آرگون از پاشش جلوگیری میکند.
دی اکسید کربن گاز ارزانی است، اما مشکلاتی هم دارد و بدون عیب و نقص نیست، بعنوان مثال دود بالایی ایجاد میکند؛ همچنین استفاده از آن باعث ایجاد قوس لرزانتر و پاشش جوش میشود. با این حال مخلوط کردن دی اکسید کربن با آرگون میتواند پراکندگی را به حداقل برساند. گاز محافظ کربن دی اکسید همچنین نباید برای فلزات نازک مانند آلومینیوم استفاده شود. زیرا تحمل گرمای آن برای فلزات نازک خیلی سخت است.
فرایند های جوشکاری با گاز محافظ
برخی از فرایندهای جوشکاری قوس الکتریکی (arc) از یک محافظ خارجی استفاده نمیکنند؛ بلکه در عوض از طریق پوشش سربارهای از جوش و گازهای حاصل از واکنشهای شیمیایی در قوس، سیستم محافظ مخصوص خود را تأمین میکنند. این فرایندها عبارتاند از: فرایند جوشکاری قوس فلزی Shielded Metal (SMAW)، فرایند جوشکاری قوس تو پودری (FCAW-S) و فرایند قوسی (SAW).
فرایندهای اصلی جوشکاری قوس الکتریکی که به گاز محافظ جوشکاری خارجی احتیاج دارند عبارتاند از:
- فرایند جوشکاری قوس الکتریکی تنگستن GTAW (فرایند TIG)
- فرایند جوشکاری قوس فلزی گازی GMAW (فرایند MIG)
- جوشکاری قوس با هسته فلزی GMAW-C (فرایند هسته فلزی)
- فرایند جوشکاری قوس محافظت شده با گاز (FCAW-G)
انواع گازهای محافظ مورد استفاده در این فرایندها بسیار زیاد است، به ویژه مخلوطهای سه قسمتی به وفور مورد استفاده قرار میگیرد و درصد هر نوع گاز در مخلوطها نیز با هم متفاوت است. علاوه بر این، گازها میتوانند بسته به منطقه جهان جوشکاری، متفاوت باشند.
متداولترین گازهای محافظ جوشکاری مورد استفاده برای این فرایندهای اصلی جوش قوس شامل آرگون (Ar)، هلیوم (He)، دی اکسید کربن (CO2) و اکسیژن (O2) است. در حالی که Ar ، He و CO2 ممکن است برای کاربردهای خاص بصورت تنها (یعنی 100٪) مورد استفاده قرار گیرند، در موارد دیگر این چهار گاز در ترکیبات مختلف با هم مخلوط میشوند تا مخلوطهای گاز محافظ تشکیل شود. نسبت این مخلوطها به صورت درصد بیان میشوند. به عنوان مثال 75٪ Ar 25٪ CO2. بعضی اوقات آنها حتی به صورت مختصر مانند “75/25” بیان میشوند.
هر یک از این گازها دارای خواص مختلفی هستند که بر نحوه واکنش آنها در اثر حرارت قوس جوش اثر میگذارند. این موارد شامل واکنش پذیری، پتانسیل یونیزاسیون و هدایت حرارتی آنها است. میزان این واکنش است که نشان میدهد آیا میتوان از گاز یا مخلوط گازها برای مواد خاصی استفاده کرد یا خیر. این خصوصیات همچنین بر ویژگیهای عملکرد گازهای محافظ جوشکاری مختلف و همچنین شکل مهره و پروفایلهای نفوذ تأثیر میگذارد.
سخن پایانی
گاز محافظ یک جزء حیاتی در جوشکاری است که با محافظت از حوضچه مذاب در برابر آلایندههای جوی، کیفیت و یکپارچگی جوشها را تضمین میکند. درک نقش و انواع گازهای محافظ برای دستیابی به نتایج جوشکاری موفق و تولید محصولات نهایی با کیفیت بالا ضروری است. تسلط بر استفاده از گاز محافظ کلید تبدیل شدن به یک جوشکار ماهر است که قادر به تولید جوش های قوی و بادوام است. هرکسی که برای ورود به حرفه جوشکاری تحصیل میکند و یا علاقمند به جوشکاری است ، باید نقش مهمی را که این گازها در جوشکاری ایفا می کنند، بداند. بهترین راه برای یادگیری نحوه استفاده از این گازها در پروژه های جوشکاری، گرفتن ابزار در دست خود فرد و حضور مربی در کنار فرد است. از اینکه در این مقاله با ما همراه بودید سپاس گزاریم. منتظر نظرات شما هستیم.
منابع : tws – lincolnelectric – bakersgas