کاهش پاشش با دستگاه جوش co2 یکی از چالشهای اصلی جوشکاران در فرآیندهای صنعتی است که تأثیر مستقیمی بر کیفیت نهایی کار، ایمنی محیط و هزینههای تولید دارد. با بهینهسازی تنظیمات دستگاه جوش CO2 و MIG (مانند ولتاژ، آمپر و سرعت تغذیه سیم) و انتخاب گاز محافظ مناسب (ترکیب Argon/CO2)، میتوان پاشش ذرات مذاب را بهطور چشمگیری کنترل کرد. استفاده از فناوریهای نوین مانند سیمجوشهای Low-Spatter و سیستمهای پالسی نیز در کاهش پاشش با دستگاه جوش co2 مؤثر است. این اقدامات نهتنها سطح جوش را تمیزتر و یکنواختتر میکند، بلکه هزینههای پاکسازی، اتلاف مواد و خطرات ایمنی را کاهش میدهد و بهرهوری کلی عملیات جوشکاری را افزایش میدهد. در این محتوا، به بررسی راهکار های جلوگیری از پاشش جوش می پردازیم.
جرقه یا پاشش جوش در جوشکاری چیست؟
پاشش جوش (Weld Spatter) به ذرات ریز و مذاب فلز اشاره دارد که در حین فرآیند جوشکاری، بر اثر ناپایداری قوس، حرارت بالا یا واکنشهای شیمیایی (مانند ترکیب CO₂ با فلز مذاب) از حوضچه جوش به اطراف پرتاب میشوند. این ذرات پس از سرد شدن به صورت دانههای سخت و چسبنده روی سطح فلز پایه، نواحی مجاور جوش یا حتی تجهیزات کارگاه مینشینند. پاشش نهتنها کیفیت ظاهری جوش را کاهش میدهد (ایجاد ناهمواری و نیاز به پرداخت اضافی)، بلکه میتواند موجب آسیب به تجهیزات، افزایش خطر آتشسوزی (برخورد به مواد اشتعالپذیر)، اتلاف مواد مصرفی و بالا بردن هزینههای تولید (پاکسازی و اصلاح سطح) شود. کنترل این پدیده، بهویژه در جوشکاری CO₂ که به دلیل ماهیت گاز محافظ مستعد پاشش بالاست، اهمیت فراوانی دارد.
چه چیزی باعث پاشش جوش در جوشکاری CO2 می شود؟
در جوشکاری CO₂ (که معمولاً به عنوان جوشکاری قوس الکتریکی با سیم توپودری تحت پوشش گاز CO₂ یا مخلوطهای حاوی CO₂ شناخته میشود)، پاشش جوش (Spatter) یکی از مشکلات رایج است. عوامل اصلی ایجاد پاشش به صورت خلاصه عبارتند از:
تنظیمات نادرست پارامترهای جوشکاری:
- ولتاژ بیش از حد بالا: باعث طولانی شدن قوس، ناپایداری قوس و تشکیل قطرات بزرگ فلز مذاب میشود که به راحتی به اطراف پاشیده میشوند.
- آمپر بیش از حد بالا: انتقال فلز مذاب را به حالت پرتابی (Explosive Transfer) تغییر میدهد که همراه با پاشش شدید است.
- سرعت تغذیه سیم نامناسب: سرعت خیلی بالا (نسبت به ولتاژ) قوس را کوتاهتر از حد بهینه میکند و احتمال چسبیدن سیم و پاشش ناگهانی را افزایش میدهد. سرعت خیلی پایین نیز میتواند باعث ناپایداری قوس شود.
- سرعت حرکت تورچ نامناسب: سرعت حرکت خیلی کم باعث تجمع حرارت و مذاب زیاد میشود. سرعت خیلی زیاد باعث کوتاه شدن قوس و پاشش میگردد.
کیفیت و شرایط گاز محافظ:
- ناخالصی یا رطوبت در گاز CO₂: رطوبت یا ناخالصی (مانند نیتروژن یا اکسیژن) در گاز محافظ، باعث ناپایداری قوس، ایجاد حباب در حوضچه مذاب و پاشش شدید میشود.
- جریان ناکافی گاز محافظ: ناتوانی در دفع اتمسفر اطراف از منطقه جوش، باعث اکسیداسیون فلز مذاب، ناپایداری قوس و افزایش پاشش میشود.
- نشت گاز (مثلاً از شیلنگ یا اتصالات): هوای اضافی وارد منطقه جوش میشود و مانند ناخالصی عمل میکند.
- فاصله زیاد نازل گاز از کار: منطقه حفاظت نشده گسترش یافته و گاز کافی به حوضچه مذاب نمیرسد.
- نازل گاز کثیف یا مسدود شده (مثلاً با پاششهای قبلی): جریان گاز را مختل کرده و محافظت ناکافی ایجاد میکند.
کیفیت و شرایط سیم جوش:
- سیم جوش مرطوب یا کثیف: رطوبت، روغن، گریس یا زنگزدگی روی سیم جوش در حین ذوب، تبخیر یا تجزیه شده و باعث انفجارهای کوچک و پاشش میشود.
- کیفیت پایین سیم جوش: ناخالصیها در ترکیب شیمیایی سیم یا ناهمواری سطح آن میتواند انتقال قطرات مذاب را نامنظم کرده و پاشش ایجاد کند.
- قطر نامناسب سیم جوش: انتخاب قطر سیم نامتناسب با پارامترهای جوشکاری (مثلاً سیم خیلی نازک برای آمپر خیلی بالا) میتواند منجر به پاشش شود.
شرایط سطح کار (فلز پایه):
- وجود آلودگی روی سطح کار: زنگزدگی، رنگ، روغن، گریس، رطوبت، اکسیدهای ضخیم یا آلودگیهای دیگر روی سطح کار، در حین جوشکاری میسوزند یا تبخیر میشوند و باعث ایجاد حباب، انفجارهای کوچک و پاشش شدید میگردند.
- وجود رطوبت: به خصوص در اتصالاتی که رطوبت در درزها وجود دارد، خطر پاشش بالا میرود.
تکنیک جوشکاری (اپراتور):
- زاویه نامناسب تورچ: زاویههای شدید تورچ (مخصوصاً در جوشکاری گوشه) میتواند باعث انحراف گاز محافظ و ناپایداری قوس شود.
- فاصله نامناسب نوک سیم تماس (CTWD – Contact Tip to Work Distance): فاصله خیلی زیاد باعث گرم شدن بیش از حد سیم، ناپایداری قوس و پاشش میشود. فاصله خیلی کم نیز خطر چسبیدن سیم را افزایش میدهد.
- حرکت نامنظم تورچ: حرکت ناپایدار تورچ (لرزش، توقفهای ناگهانی) قوس را ناپایدار کرده و پاشش ایجاد میکند.
عوامل محیطی:
- وجود جریان هوا یا باد: باد حتی ملایم میتواند گاز محافظ را پراکنده کرده و محافظت ناکافی ایجاد کند که منجر به ناپایداری قوس، اکسیداسیون و پاشش میشود.
با کنترل این عوامل (استفاده از گاز خشک و خالص، تنظیم دقیق پارامترها، تمیزکاری کامل سطح کار و سیم جوش، نگهداری صحیح تجهیزات، استفاده از تکنیک مناسب و محافظت در برابر باد) میتوان پاشش جوش را به میزان قابل توجهی کاهش داد.
برای آموزش جامع جوش Co2 کلیک کنید.
چرا جلوگیری از پاشش جوش در جوشکاری CO2 مهم و حیاتی است؟
- پاشش علاوه بر افزایش هزینه های تولید, اتلاف سیم جوش، افزایش مصرف گاز و زمان بری تمیزکاری سطح کار را نیز در پی دارد.
- تهدید کیفیت اتصال جوش با ایجاد نقاط ناقص، ناپیوستگی و آلودگی سطح کار
- جلوگیری از کاهش ایمنی اپراتور و محیط کار با پاشش فلز داغ خطر سوختگی، افزایش خطر آتشسوزی و آسیب به تجهیزات
- کنترل پاشش بهره وری را بهبود بخشیده و نیاز به عملیات تکمیلی پرهزینه مانند سنگزنی یا پرچ کاری را کاهش میدهد، که در نهایت به جوشی تمیزتر، مستحکمتر و مقرونبهصرفه منجر میشود.
روش های کاهش پاشش با دستگاه جوش co2
برای کاهش پاشش (Spatter) در جوشکاری CO₂ (معمولاً به عنوان جوشکاری MIG شناخته میشود)، باید عوامل مختلفی از تنظیمات دستگاه تا تکنیک اجرا را کنترل کنید. در ادامه، روشهای مؤثر به طور کامل توضیح داده شده اند:
1. تنظیم پارامترهای جوشکاری
- ولتاژ و آمپر مناسب: ولتاژ بالا باعث پاشش زیاد میشود. ولتاژ را طبق جداول مرجع برای ضخامت فلز و قطر سیم تنظیم کنید.
- آمپر (سرعت تغذیه سیم) را طوری تنظیم کنید که قوس پایدار بماند (اغلب ۱۸۰–۲۲۰ آمپر برای فولاد نرم).
- سرعت جوشکاری: سرعت حرکت تورچ باید متناسب با آمپر باشد. سرعت کم و حرارت اضافی موجب پاشش بیشتر میشود.
2. انتخاب گاز محافظ مناسب
- ترکیب گاز: استفاده از CO₂ خالص پاشش بیشتری ایجاد میکند. ترکیب آن با آرگون (مثلاً C25: 75% Ar + 25% CO₂) پاشش را تا ۵۰% کاهش میدهد.
- دبی گاز: دبی معمولاً ۱۵-۲۰ لیتر/دقیقه است. دبی کم موجب عدم محافظت کافی و پاشش و تخلخل شده و دبی زیاد باعث تلاطم گاز و پاشش میشود.
3. تنظیم طول قوس (Stickout)
- فاصله نوک نازل تا قطعه کار (CTWD) باید ۱۰-۱۵ میلیمتر باشد.
- طول قوس بیش از حد باعث افزایش مقاومت الکتریکی , گرمای زیاد و پاشش میشود.
- طول قوس کوتاه امکان چسبیدن سیم به نوک تماسی (Contact Tip).را در پی دارد.
4. نگهداری تجهیزات
- نوک تماسی (Contact Tip):ساییدگی یا کثیفی نوک، قوس را ناپایدار کرده و باعث پاشش میشود. آن را هر ۸ ساعت کاری بررسی و تعویض کنید.
- کابلها و اتصالات: اتصالات شل یا کابلهای فرسوده مقاومت را افزایش داده و پاشش ایجاد میکنند.
- نازل گاز: پاششهای جامد روی نازل، جریان گاز را مختل میکنند. نازل را با عامل ضد پاشش یا برس سیمی تمیز کنید.
5. استفاده از تجهیزات ضد پاشش
- اسپری یا ژل ضد پاشش: سطح قطعه کار یا نازل را با این مواد بپوشانید تا پاششها به قطعه نچسبند.
- نازلهای سرامیکی یا با پوشش تفلون: پاششها به این سطوح کمتر میچسبند.
نکته: باقیمانده این مواد باید پس از جوشکاری پاک شود (ممکن است روی رنگ یا پوشش تأثیر بگذارد).
6. تکنیک اجرای جوش
- زاویه تورچ: زاویه ۱۵-۲۰ درجه نسبت به سطح کار (در جهت جوش یا مخالف آن) را حفظ کنید.
- حرکت تورچ: حرکت زیگزاگ یا دورانی کنترل شده پاشش را کاهش میدهد.
- فاصله از سطح کار: تورچ را بیش از حد به قطعه نزدیک نکنید (فاصله ایده آل: ۱۰-۱۵ میلیمتر).
7. کیفیت مواد مصرفی
- از سیم های پاک سازی شده (Cleaned) استفاده کنید.
- سیمهای ارزان قیمت ممکن است ناخالصی داشته باشند که پاشش را افزایش میدهد.
- سطح کار باید عاری از زنگزدگی، روغن یا رطوبت باشد. پیش گرمایش (۱۰۰-۱۵۰°C) برای قطعات ضخیم توصیه میشود.
8. کنترل محیط جوشکاری
- باد یا تهویه شدید گاز محافظ را پراکنده میکند. از پاراوان یا محیط بسته استفاده کنید.
- رطوبت بالا باعث پاشش و تخلخل میشود. سیم جوش و قطعه کار باید خشک باشند.
9. استفاده از تکنولوژیهای پیشرفته
- استفاده از جوشکاری پالسی (Pulse MIG):که امکان کنترل دقیق انتقال قطرات سیم و پاشش نزدیک به صفر را فراهم میکند.
- استفاده از دستگاه جوش اینورتر با کنترل دیجیتال
- سیمهای ویژه: استفاده از سیمهای فلکسکور (Flux-Cored) پاشش کمتری دارند (اما نیاز به تنظیمات خاص دارند).
10. کالیبراسیون دستگاه
- تست روی قطعه ضایعات: پیش از جوشکاری اصلی، پارامترها را روی نمونه مشابه تنظیم کنید.
- بررسی قوس: صدای قوس باید یکنواخت باشد. صدای ترکیدن نشانه تنظیمات نادرست است.
دستگاه جوش CO2 و MIG وینر؛ جوشی یکدست، پاششی نزدیک به صفر!
با فناوری پیشرفته اینورتر دیجیتال و سیستم انتقال قطرات بهینهشده، دستگاههای وینر پاشش جوش را تا ۷۰% کاهش میدهند. ترکیب هوشمند کنترل پالسی (Pulse Control)، ولتاژ پایدار و طراحی نازلهای ضدچسبندگی، نهتنها کیفیت جوش را ارتقا میبخشد، بلکه زمان پاکسازی پس از کار و هزینههای مصرفی را بهشدت کاهش میدهد. برای جوشکاریهای سریع، تمیز و حرفهای روی فولاد (از قطعات خودرو تا سازههای صنعتی) وینر انتخاب حرفه ایهاست. تجربه جوشی نرم، بدون پاششهای آزاردهنده!
مزایای کلیدی:
- صرفهجویی در سیم جوش و گاز محافظ
- سطح جوش یکنواخت بدون سربارهی اضافی
- گارانتی و خدمات پس از فروش معتبر
معرفی دستگاه جوش میگ دبل پالسی آلومینیوم وینر مدل 3850:
دستگاه جوش میگ مدل 3850 قابلیت جوش کاری انواع فلزات خصوصا آلومینیوم را دارد و با بهره گیری از سیستم محافظ اضافه ولتاژ و اضافه جریان, مناسب جوشکاری ورق با ضخامت 0.8 تا 1.2 میلیمتر می باشد.
دارای:
- تورچ CO2
- کابل جوش
- وایرفیدر
- یونیت آب خنک
- ترولی
- انبر اتصال
- کابل جوش،برق و شلنگ
- دو غلطک V1.2-1
- دو غلطک بدون شیار
- بست و پیچ
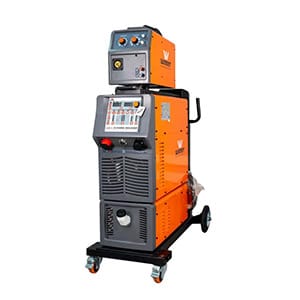
معرفی دستگاه جوش اینورتر 140 آمپر وینر مدل 7011 :
- مناسب جوشکاری ورق های گالوانیزه و جوشکاری ورق های نازک
- راحتی کار برای افراد کم تجربه
- سرعت بالای جوشکاری
- مناسب برای تعمیرات و بازسازی تجهیزات و جوشکاری های ظریف
- مناسب برای محیط های کارگاهی و تولیدی
- دارای: کابل جوش , تورچ co2 , انبر اتصال , انبر جوش ماسک و شیشه
نتیجه گیری
اکنون اقدامات کافی برای کاهش پاشش با دستگاه جوش co2 را به همراه دارید. کاهش پاشش جوش در فرآیند CO2، صرفاً یک هدف عملیاتی نیست، بلکه گام بلندی به سوی تسلط بر هنر ظریف جوشکاری است. با بهکارگیری دقیق تنظیمات بهینه دستگاه جوش CO2 و MIG (همچون ولتاژ و آمپر مناسب، سرعت حرکت صحیح، فاصله قوس ایدهآل و گاز محافظ کافی)، انتخاب دقیق سیم جوش (مانند سیمهای کم پاشش یا دارای پوشش خاص) و رعایت اصول پیشرفتهای مانند زاویهگیری صحیح الکترود و تمیزی بینقص سطح کار، نهتنها میتوان پاششهای آزاردهنده و هزینهبر را به حداقل رساند، بلکه کیفیت جوش را بهطور چشمگیری ارتقاء داد.
این مهارتهای فنی، در کنار تمرین مستمر و درک عمیق از رفتار حوضچه جوش، شما را از یک اپراتور به یک جوشکار ماهر تبدیل میکند؛ هنرمندی که بر چالشهای جوش CO2 چیره شده و قادر به خلق اتصالاتی مستحکم، تمیز و با دوام است. تسلط بر این جزئیات، همان نقطهتمایز بین جوشکاری معمولی و هنر جوشکاری حرفهای محسوب میشود.